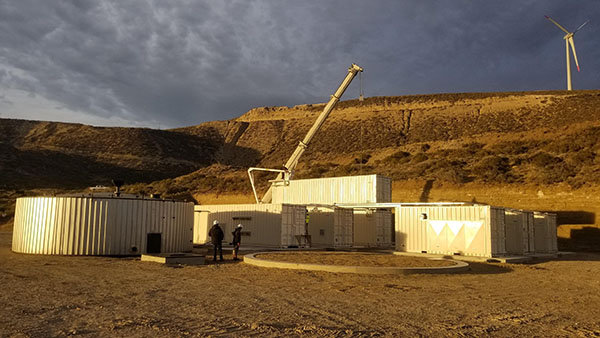

Compañías Asociadas Petroleras (Capsa-Capex) extrajo en julio 2.979 metros cúbicos diarios de crudo. La firma argentina controlada por la familia Götz es la quinta productora del país detrás de YPF, Pan American, Pluspetrol y Vista. Un método de trabajo eficiente, acompañado por inversión en tecnología de punta y el compromiso de su personal, le permitió hacerse un lugar entre los grandes jugadores del sector, aunque sus dueños prefieren mantener el perfil bajo. El punto fuerte de la empresa en el Golfo San Jorge es el yacimiento Diadema, un campo maduro con más de 100 años de historia donde lograron maximizar el rendimiento a partir de la aplicación de técnicas de recuperación terciaria mediante métodos químicos. Hasta el año pasado, la empresa trabajó allí con entre 12 y 14 equipos torre, para perforación, pulling y workover.
Desde la empresa indicaron a TRAMA que el manejo de costos es central para poder defender la rentabilidad de campos maduros. «La mejora continua de la eficiencia y los costos para lograr competitividad, aun frente a las variaciones del mercado en los precios del crudo, nos ha permitido mejorar los factores de recuperación, incorporar nuevas tecnologías –como es el caso de polímeros–, desarrollar nuevos horizontes geológicos y trabajar junto con nuestros proveedores de servicios y herramientas en el desarrollo de productos que nos permitan alcanzar los objetivos perseguidos. Estas acciones concretas, junto con el compromiso de nuestra gente, conforman la base de nuestra estrategia».
Al ser consultados sobre cuáles fueron los principales hitos operativos que apuntalaron su desarrollo, respondieron: «Ordenar la operación e ir armando una base de datos que nos permita medir y gestionar. Una operación ordenada no significa incrementar los costos, y para gestionar es necesario contar con información». «A partir de ello se fueron desarrollando herramientas para bajar, por ejemplo, los costos de cantidad de intervenciones dadas las características más reiteradas de fallas como es nuestro sistema STL; o los análisis de Technical Limit que constantemente realizamos con nuestros contratistas de equipos torre a fin de eficientizar las operaciones; o los desarrollos con nuestro personal de plantas junto con los proveedores de productos químicos a fin de bajar los costos de tratamiento, ya sea trabajando sobre los productos en sí mismos como también en los procesos», agregaron. Además de la inversión continua, en CAPSA destacan como otro factor distintivo su política de recursos humanos, que conlleva a un compromiso de la gente con la empresa, un activo indispensable para encarar cualquier desafío productivo.

El origen
El yacimiento Diadema se ubica en las afueras de Comodoro Rivadavia, en la provincia de Chubut. Le debe su nombre al pueblo Diadema Argentina, que comenzó como un campamento montado por Royal Shell Dutch en 1917 cuando desembarcó en la Cuenca del Golfo San Jorge para explorar su primera concesión exploratoria. La firma angloholandesa descubrió petróleo allí a fines de 1925, para luego iniciar un largo período de explotación.
En 1977 Shell le vendió el yacimiento a la Compañía Austral Petrolera SA, una sociedad constituida por tres empresas más pequeñas denominadas Competrol SA, Técnica Patagónica SA y Servicios Ryder Scott SA. Esa firma pasaría a llamarse luego Compañías Asociadas Petroleras Sociedad Anónima (CAPSA), que continúa hasta hoy a cargo de la explotación del campo.
Para sorpresa de muchos, CAPSA revirtió la situación de virtual abandono en la que estaba el yacimiento cuando se hizo cargo y fue incrementando de manera notable los niveles de producción.

Recuperación terciaria
El último logro de CAPSA en Diadema fue el incremento de la productividad a partir de técnicas de recuperación terciaria. Si la explotación primaria no prevé ningún tipo de asistencia al reservorio y la secundaria implica la inyección de agua para barrer mejor los sistemas hidrocarburíferos, la terciaria contempla una amplia gama de soluciones –vapor, geles, CO2, químicos, entre otros métodos– que apuntan a mejorar la eficiencia volumétrica de barrido y movilizar el petróleo bypassedo por la secundaria. En ese metié, CAPSA avanzó más que cualquier otra petrolera. Al menos en la Argentina. De los 1.850 metros cúbicos diarios (m3/d) de crudo que producía el año pasado Diadema, unos 380 m3/d los estaba extrayendo por medio de la inyección de polímeros en la formación.
La Cuenca del Golfo San Jorge posee una condición que permite este tipo de emprendimientos: su bajo nivel de salinidad en el agua de formación y reservorios someros con temperaturas menores a 80 °C. En Chubut y en el norte de Santa Cruz es común encontrar reservorios con una salinidad cercana a 15.000 ppm de TDS. En Neuquén, ese indicador puede superar los 100.000 ppm. La operadora empezó a estudiar la tecnología e inició un proyecto piloto en 2007 en Diadema.
En promedio, la empresa precisaba producir y reinyectar 50 m3 de agua para producir 1 de petróleo. Esa estadística comprometía la continuación de la explotación secundaria del área. Esa realidad empujó a la operadora a evaluar la tecnología de la recuperación terciaria en el yacimiento.
La Argentina no tiene tradición en este tipo de proyectos. Apenas existen tres iniciativas de recuperación terciaria con algo de historia en el país: la de CAPSA en Chubut; la de YPF en Manantiales Behr, en la misma provincia; y la de Pluspetrol, en el yacimiento El Corcobo, en la Cuenca Neuquina, aunque las dos últimas aún en instancia de estudio.
El proyecto del grupo es el más avanzado, por distancia. En la etapa piloto, que se extendió por unos cinco años, se probaron los resultados de la implementación. Después se ajustó la economía del emprendimiento. Con los polímeros se buscó mejorar la eficiencia de barrido produciendo un cambio en las líneas de flujo y tratar de lograr un aumento en el factor de recuperación.

Mayor eficiencia
Así como YPF debió transitar una compleja curva de aprendizaje para descifrar la rentabilidad de la explotación no convencional en Vaca Muerta, la compañía recorrió un proceso de optimización constante cuando lanzó la producción terciaria. Lo hizo casi en soledad, dado que el conocimiento disponible en el país sobre esta tecnología era exiguo. Hoy en día, la empresa inyecta cerca de 16 toneladas de polímeros por día en 5.000 m3 de agua (que es producida en los mismos pozos productores del proyecto). A partir de eso, pudo incrementar en forma disruptiva la viscosidad del fluido de inyección, que hoy oscila entre los 70 y los 130 centipoise (cp) en las zonas alcanzadas por el proyecto.
La empresa comenzó con viscosidades de 20 cp y fue subiendo debido a que la producción declinaba y tenía que incrementar la inversión agregando más producto para mantener la producción y además ir a nuevas zonas. El concepto fue lograr empujar hidrocarburos con un producto que tuviera una viscosidad similar al petróleo.
Desde un primer momento, se puso el acento tanto en la eficiencia de la tecnología como en los costos de su implementación. La necesidad de mantener bajo control los costos impulsó a la compañía a buscar soluciones creativas y novedosas. En lugar de apelar a un proveedor internacional, la petrolera diseñó y desarrolló su primera planta de inyección de polímeros en conjunto con Sabinur, una empresa local. La firma se caracteriza por apoyarse en sus proveedores para encontrar soluciones que se ajusten a su presupuesto. Es un rasgo que caracteriza a las petroleras independientes a nivel mundial, que a veces no pueden costear lo que cobran las grandes empresas de servicios e insumos de la industria petrolera.
Los polímeros se caracterizan también por su inestabilidad. No pueden utilizarse los sistemas de regulación de caudal convencionales (válvulas e instalación selectiva) porque se rompen. Lo ideal, en proyectos de recuperación terciaria, es contar con una bomba para cada pozo inyector a fin de distribuir caudales. Pero de nuevo, eso genera un costo excesivo en áreas maduras. Por eso, los técnicos de la empresa diseñaron un rulo de caño para regular el caudal. Su costo y mantenimiento es muy inferior al de una bomba tradicional.
La gran heterogeneidad de la formación también provoca canalizaciones a nivel de reservorio en zonas poco consolidadas por formación de wormholes. Por eso, la petrolera optó por inyectar geles que se posicionan bloqueando ese canal y restaurando la eficiencia de barrido. Otro problema que debió resolver fue la distribución vertical; el polímero se rompe al pasar por una instalación selectiva, por lo que la operadora diseñó un sistema de fondo que permite distribuir el agua sin romperse hasta en tres niveles. ×
La entrada El silencioso camino de CAPSA para convertirse en el quinto productor de petróleo se publicó primero en EconoJournal.
, [#item_author]